Metals are important materials that have been used for centuries in various industries. The manufacturing process of metals involves casting and seamless rolled ring forging. Two popular forms of metal shapes that are commonly used are ingots and billets.
Although they may appear similar, there are significant differences between the two in terms of size, shape, and applications. In this article, we will discuss the differences between ingots and billets and their various applications in different industries.
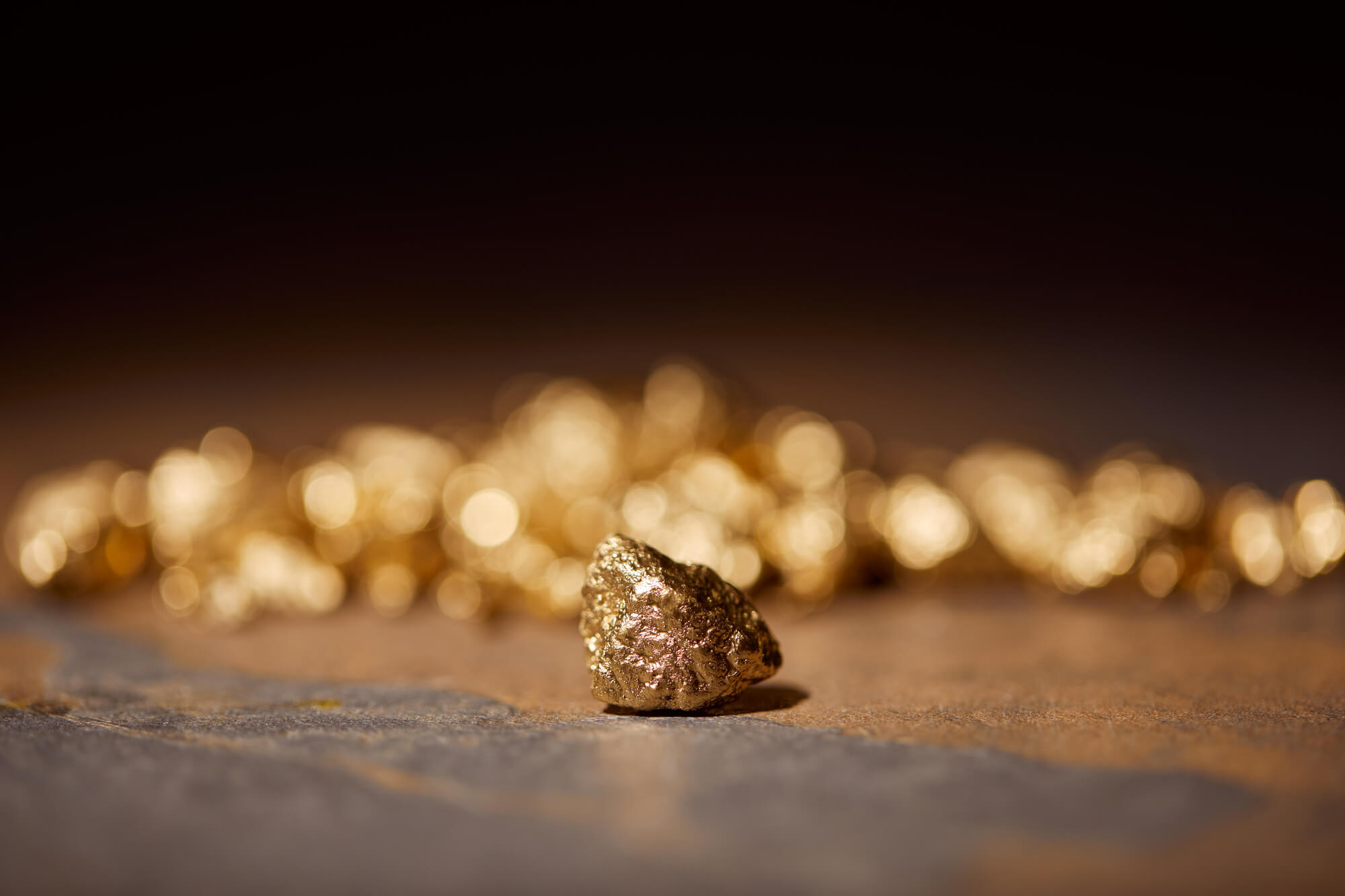
Ingot vs. Billet
What Is an Ingot?
An ingot is a metal cast into a specific shape that is easy to transport and store. The casting process involves pouring molten metal into a mold to create a solidified shape. Ingots are typically rectangular or cylindrical in shape and are commonly made from aluminum, copper, steel, and other metals. The size of an ingot can range from a few ounces to several tons depending on the metal and the manufacturing process used.
Ingot Applications
Ingots are typically used in the production of various metal products such as sheet metal, wire, and tubing. They are also used in the manufacturing of parts for machinery and equipment. The automotive and aerospace industries use ingots extensively to create components and parts for their vehicles.
What Is a Billet?
A billet is a metal cast in a cylindrical or square shape with a cross-sectional area smaller than that of an ingot. Billets are commonly used in the production of bars, rods, and tubes, which require a smaller cross-sectional area. Billets are often produced through the extrusion process, which involves forcing a metal through a die to create the desired shape.
Billet Applications
Billets are widely used in the construction industry for the production of beams, columns, and other structural components. They are also used in the production of various components and parts for machinery and equipment. Billets are commonly used in the manufacturing of gears, shafts, and axles.
Ingot vs. Billet: Differences and Applications
The main difference between ingots and billets is their size and shape. Ingots are larger and have a rectangular or cylindrical shape, while billets are smaller and typically have a square or cylindrical shape. Ingots are typically used to produce sheet metal, wire, tubing, and large components for machinery, while billets are used to produce smaller components such as gears, shafts, and axles.
In terms of manufacturing, ingots are usually created through casting, while billets are created through extrusion. Ingots are solidified in a mold, while billets are formed through the extrusion process, which involves forcing molten metal through a die to create the desired shape.
Another significant difference between the two is the cost. Ingots are more expensive to produce due to their larger size and the casting process used. Billets, on the other hand, are less expensive to produce due to their smaller size and the extrusion process used.
Are Ingots and Billets Used Interchangeably?
Ingots and billets are not necessarily used interchangeably, as they have different sizes, shapes, and applications. However, in some cases, they may be used in similar applications or processes, which may lead to confusion or the perception that they can be used interchangeably.
For example, in the steel industry, both ingots and billets may be used as raw materials for the production of various steel products. In this context, they may be seen as interchangeable in terms of their use as a starting material for further processing.
In addition, some industries may use different terminology for similar metal shapes, which may lead to further confusion. For instance, in the aluminum industry, a billet may refer to a larger rectangular shape, while a smaller cylindrical shape may be referred to as a rod or a bar.
Overall, while there may be some overlap in the applications or terminology of ingots and billets, they are distinct shapes with unique characteristics and are typically used for different purposes in manufacturing and production.
How Are Ingots Used in Rolled Ring Forgings?
Ingots are one of the primary raw materials used in the rolled ring forging process. The ingots are typically made of a specific type of metal or alloy that is chosen for its desired properties, such as strength, durability, and corrosion resistance.
To begin the rolled ring forging process, a piece of the ingot is heated to a specific temperature, which can vary depending on the type of metal being used. The heated ingot is then placed onto a mandrel or shaping tool and rolled into a cylindrical shape using a specialized rolling machine. As the ingot is rolled, pressure is applied to shape it into the desired ring shape.
Once the initial rolling is complete, the partially formed ring is reheated and placed onto a larger mandrel. The rolling process is then repeated, with the pressure gradually increased to shape the ring to its final dimensions. The rolling process also helps to refine the grain structure of the metal, which can increase its strength and durability.
After the final rolling stage, the ring is cooled and then subjected to a series of finishing processes, which can include machining, heat treatment, and surface treatments. These processes help to ensure that the ring meets the required specifications for its intended use.
Overall, ingots play a critical role in the rolled ring forging process, providing the raw material needed to create strong and durable metal rings for a wide range of applications.
Billets can also be used in the rolled ring forging process, similar to ingots. Billets are typically smaller and more uniform in size and shape than ingots, and they are often preferred for smaller, precision components.
To begin the rolled ring forging process with billets, a piece of the billet is heated to a specific temperature, depending on the type of metal or alloy being used. The heated billet is then placed onto a mandrel or shaping tool, and the rolling process begins.
As with ingots, the billet is rolled into a cylindrical shape, applying pressure to shape it into a ring. The partially formed ring is then reheated and placed onto a larger mandrel to continue the rolling process. The pressure is gradually increased to shape the ring to its final dimensions, and the rolling process can help refine the grain structure of the metal.
Once the final rolling stage is complete, the ring is cooled and then subjected to finishing processes such as machining, heat treatment, and surface treatments. These processes help ensure that the ring meets the required specifications for its intended use.
The use of billets in the rolled ring forging process can offer several advantages over ingots, such as increased efficiency and cost-effectiveness. Billets are often more readily available than ingots and require less processing to reach the desired shape and dimensions. Additionally, the use of billets can result in less material waste, making it a more sustainable option for some projects.
Overall, both ingots and billets can be used in the rolled ring forging process to create strong and durable metal rings for a wide range of applications. The choice between ingots and billets often comes down to the specific requirements of the project, such as the size and quantity of the components needed and the available budget.
Learn More About Seamless Rolled Ring Forging
Ingots and billets are two commonly used metal shapes that have different sizes, shapes, and applications. Ingots are larger and commonly used in the production of sheet metal, wire, tubing, and large components for machinery.
Billets are smaller and commonly used in the production of gears, shafts, and axles. Understanding the differences between the two can help manufacturers choose the appropriate metal shape for their specific application. Feel free to contact us if you have any more questions.
//php comments_template( '', true ); ?>