There are several distinct kinds of forging. In rolled ring forging, a thick, round piece of metal is punched, and then that portion is rolled and squeezed into a thin ring. In closed die forging, two dies are moved closer to one another until they completely enclose the workpiece and produce the required item. Open die forging is the next process that will be explained in this blog post.
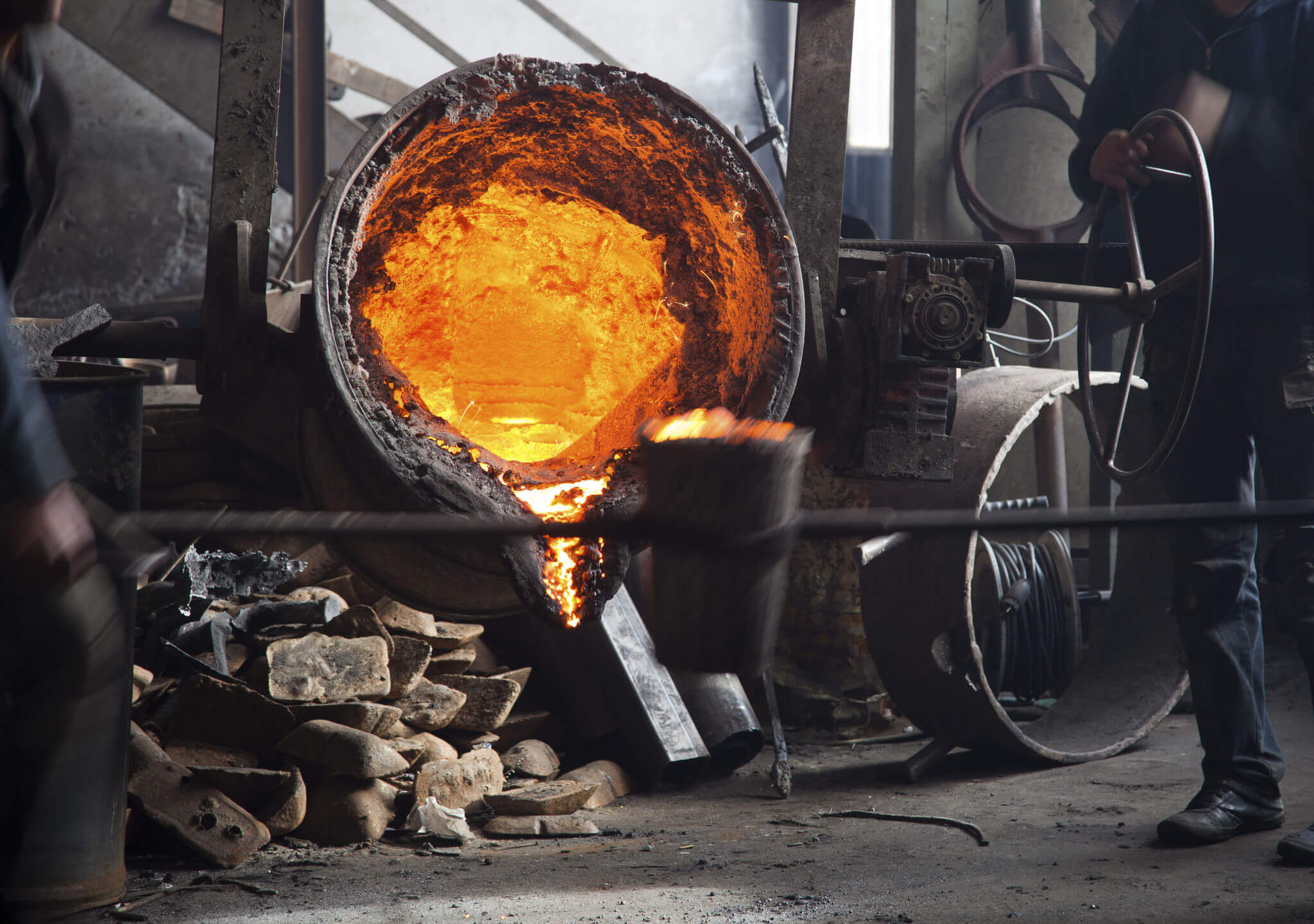
Open Die Forging in Just a Few Minutes
Process
In open die forging, metal pieces are heated between a top die connected to a ram and a bottom die to distort them. The metal is gently pressed into or hammered into the correct shape while being processed at temperatures between 500 and 2400 °F. To acquire the tolerances for finished standards, the process typically needs a second machine or refinement.
Benefits
Open die forging is advantageous even if it requires more labor. Both basic and sophisticated pieces can be made using it, including:
- Shafts
- Cylinders
- Rings
- Sleeves
- Discs
One of the main advantages of this kind of forging is that the metal is repeatedly worked, increasing its strength and final product’s grain structure. Over and above, it improves the product’s resistance to fatigue and decreases voids.Because the physical qualities of the metal are enhanced and developed during the forging process, open die forging results in a metal creation that has distinctive physical features. This indicates that as the metal’s grain structure is improved, its density rises, which increases its total strength. In addition, the metal’s grain flow is changed in a way that allows it to counterbalance, accept, and neutralize the stress load burden of a finished part or assembly.
In Search of Quality Open Die Forging?
Contact us right away if you want to use open die forging to produce metal parts for your upcoming project.
//php comments_template( '', true ); ?>