In the quest for efficiency and performance, industries across the globe are constantly seeking innovative ways to manufacture lightweight, high-strength components. One manufacturing method that has gained significant traction in recent years is aluminum die casting. With its exceptional properties and numerous advantages, aluminum die castings have emerged as a go-to solution for producing lightweight yet robust parts. In this article, we will explore the benefits of aluminum die machined castings and how they contribute to the mass production of high-strength components.
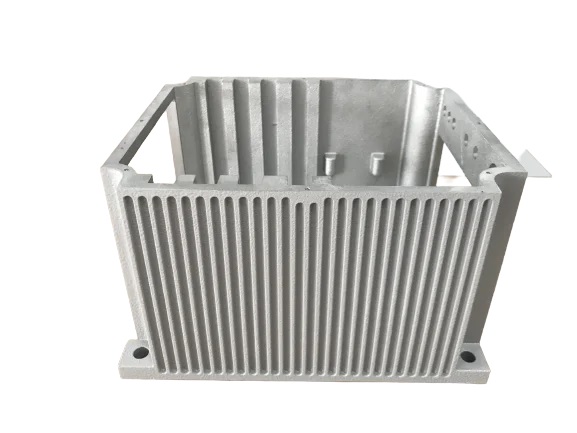
Remarkable Strength-to-Weight Ratio
One of the most significant advantages of aluminum die castings is their remarkable strength-to-weight ratio. This property makes them highly sought after in industries where weight reduction is a critical factor without compromising structural integrity. Let’s delve deeper into this aspect and explore why the strength-to-weight ratio of aluminum die castings is so exceptional.
1. High Strength
Aluminum die castings possess excellent strength properties, allowing them to withstand substantial loads and stresses. The die-machined casting process involves injecting molten aluminum under high pressure into a precisely designed permanent mold. This rapid cooling and solidification process results in a fine-grained microstructure with a homogeneous distribution of the aluminum alloy’s reinforcing elements. Consequently, the resulting castings exhibit enhanced strength and mechanical properties.
2. Material Optimization
The die casting machining process allows for precise control over the casting design and material distribution, facilitating material optimization for maximum strength and minimal weight. Engineers can strategically place material in areas subjected to higher stress, ensuring optimal load-bearing capabilities while minimizing material usage in non-critical areas. This ability to tailor the component’s structure and thickness enables the creation of lightweight parts without sacrificing strength, resulting in an outstanding strength-to-weight ratio.
3. Enhanced Performance
The remarkable strength-to-weight ratio of aluminum die castings contributes to improved overall performance in various industries. In automotive applications, lighter components lead to increased fuel efficiency, reduced emissions, and improved handling. In aerospace, weight reduction translates into enhanced maneuverability, increased payload capacity, and improved range. Moreover, the high strength of aluminum die castings allows for the production of complex and intricate parts that can withstand demanding operating conditions while maintaining their structural integrity.
Design Flexibility
Design flexibility is a significant benefit of aluminum die castings, offering engineers and designers immense freedom to create intricate and complex geometries that may be challenging or expensive to achieve using other manufacturing methods. Let’s explore the various aspects of design flexibility provided by aluminum die castings.
1. Complex Geometries
Aluminum die casting allows for the production of components with intricate and complex shapes. The process involves injecting molten aluminum into a precisely designed mold under high pressure. This enables the replication of intricate details, such as thin walls, sharp corners, fine features, and undercuts. The ability to create complex geometries opens up new design possibilities, allowing for innovative and efficient part designs that maximize performance and functionality.
2. Dimensional Accuracy and Consistency
The die casting process offers exceptional dimensional accuracy and consistency in part production. The use of precision molds ensures that each casting is replicated with high fidelity, resulting in consistent part dimensions and tolerances. This level of accuracy is particularly vital in applications where tight tolerances are required for proper fit and functionality. By achieving precise dimensions consistently, aluminum die castings reduce the need for additional CNC machining or post-processing, saving time and cost in the manufacturing process.
3. Surface Finish and Aesthetics
Aluminum die castings typically exhibit excellent surface finishing right out of the mold, reducing the need for additional surface treatments. The molds used in the die casting process impart a smooth surface texture to the castings, resulting in aesthetically pleasing parts. This advantage is particularly relevant in consumer electronics and automotive industries, where the visual appearance of the components plays a crucial role in the overall product appeal
Excellent Surface Finish
One of the notable benefits of aluminum die castings is their ability to achieve an excellent surface finish, often requiring minimal or no additional surface treatment. The die casting process itself contributes to the production of castings with smooth and aesthetically pleasing surfaces. Let’s explore the factors that contribute to the excellent surface finish of aluminum die castings.
1. Precision Molds
Aluminum die casting utilizes precision molds, also known as dies, that are created with high accuracy. These molds are designed to replicate the desired geometry and surface details of the component being manufactured. The high precision of the molds ensures that the molten aluminum fills the mold cavity uniformly, resulting in castings with consistent surface finish and dimensional accuracy. The molds also help in minimizing defects such as porosity or surface irregularities, ensuring a smoother surface finish.
2. Fine Casting Grain Structure
During the die casting process, molten aluminum is injected into the mold at high pressure and rapidly cools to solidify the component. This rapid cooling rate contributes to the formation of a fine-grained microstructure within the casting parts. The fine grain structure enhances the overall surface finish of the part, resulting in a smoother surface texture. The smaller grain size reduces the visibility of grain boundaries and imperfections, leading to an improved visual appearance.
3. Reduced Surface Defects
The controlled die casting process minimizes the occurrence of surface defects such as shrinkage, warpage, or porosity. The high-pressure injection of molten aluminum into the mold cavity ensures that the material fills the mold, reducing the chances of voids or imperfections on the surface. The absence of significant defects contributes to a smoother surface finish, eliminating the need for extensive surface treatments or rework.
Superior Thermal Conductivity
Superior thermal conductivity is a significant benefit of aluminum die castings, making them an ideal choice for applications that require efficient heat dissipation. The excellent thermal conductivity of aluminum allows for effective heat treatment, resulting in improved thermal management and enhanced component performance. Let’s explore the reasons why aluminum die castings exhibit superior thermal conductivity.
1. High Thermal Conductivity
Aluminum is renowned for its high thermal conductivity, which refers to its ability to conduct heat efficiently. Compared to other commonly used metals in die casting, such as steel or iron, aluminum possesses significantly higher thermal conductivity. The thermal conductivity of aluminum enables the rapid and efficient transfer of heat from the source to other parts of the component or the surrounding environment.
2. Effective Heat Dissipation
In applications where heat generation is a concern, such as in electronic devices or high-performance machinery, effective heat dissipation is crucial to maintain optimal operating temperatures. Aluminum die castings excel in dissipating heat due to their high thermal conductivity. The excellent heat transfer properties of aluminum allow for the efficient removal of thermal energy, preventing the accumulation of heat that can potentially damage sensitive electronic or mechanical components.
3. Enhanced Component Reliability and Longevity
Effective heat dissipation achieved through superior thermal conductivity contributes to improved reliability and longevity of components. By keeping operating temperatures within optimal ranges, aluminum die castings mitigate the risk of thermal stress, material degradation, and premature failure. The ability of aluminum to efficiently transfer heat away from critical components ensures its durability and extends its service life, particularly in demanding applications with high-temperature environments.
Do You Need Aluminum Die Machined Castings?
Aluminum die castings have emerged as a preferred solution for producing lightweight, high-strength components in various industries. By harnessing the benefits of aluminum die castings, industries can push the boundaries of engineering, realizing advancements in automotive, aerospace, electronics, and many other fields, while simultaneously reducing weight, improving durability, and enhancing overall product quality.
With Ferralloy Inc., you are guaranteed the best products on the market! Call us now for orders!
//php comments_template( '', true ); ?>